Redirecting to
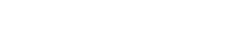
Operations commonly referred to as pick (gripping products with a robot) and place (placing them) are basic tasks in most robot applications, whether in industrial sectors (machine feeding, assembly and pallet placing/removal) or service sectors (agriculture and household). These automatic processes are highly consolidated in certain structured (limited and invariable) environments that use specific types of parts.
However, this is not the case when parts have to be handled in a wide range of conditions and in more fragmented settings (varied and unrestricted). In these kinds of applications, commercial solutions like bin picking do not apply because it is not feasible to provide settings for the thousands of references that have to be handled.
With this in mind, the Tekniker technological centre, a member of the Basque Research and Technology Alliance, has developed new artificial vision algorithms within the European PICK-PLACE project that allow industrial robot applications to identify gripping points on unknown objects arranged inside boxes.
“The system we have developed is based on Deep Learning techniques and can directly predict gripping points on objects without identifying them. This presents a flexible solution capable of handling a wide variety of objects”, explained Ander Ansuategi, a researcher at Tekniker.
Moreover, Tekniker has coordinated the technical division of the project and worked on a system that monitors the work area shared by technicians and robots.
“The intention is to make progress in robot strategies linked to artificial vision, flexible gripping and handling, precision and reliability of operations to overcome challenges associated with handling complex products with short production times in the logistics sector”, Ander added.
Software integration
Two pilot cases have been carried out throughout the initiative to verify the degree of effectiveness of the artificial vision system designed by Tekniker.
On one hand, the software that has been developed was integrated in an automated order preparation and return system used in ULMA Handling Systems, which is the project coordinator. On the other hand, the system was also tested in the preparation of spare parts orders for the distribution network of TOFAS, an automobile manufacturer belonging to the FIAT Group.
If the project is successful, it will mean the transfer of advanced Artificial Intelligence technologies to the industry through the generation of automation and robot solutions for applications such as preparing orders per unit or machine feeding, among others. The researchers at Tekniker are now working on the integration of the software in the bin picking solution developed by Tekniker.
The PICK-PLACE initiative (flexible, safe and dependable robotic part handling in industrial environments) is set to be completed in 2021 and is a project financed by the European Union Horizon 2020 program, focused on developing technologies in the field of complex product gripping and handling.
Tekniker has been working on the initiative alongside ULMA Handling Systems, CNR-STIIMA, Fraunhofer IFF, Mondragon Assembly and the Turkish automobile manufacturer TOFAS.
Subscribe to our newsletter. Just insert your e-mail and you will receive the latest news.
Redirecting to